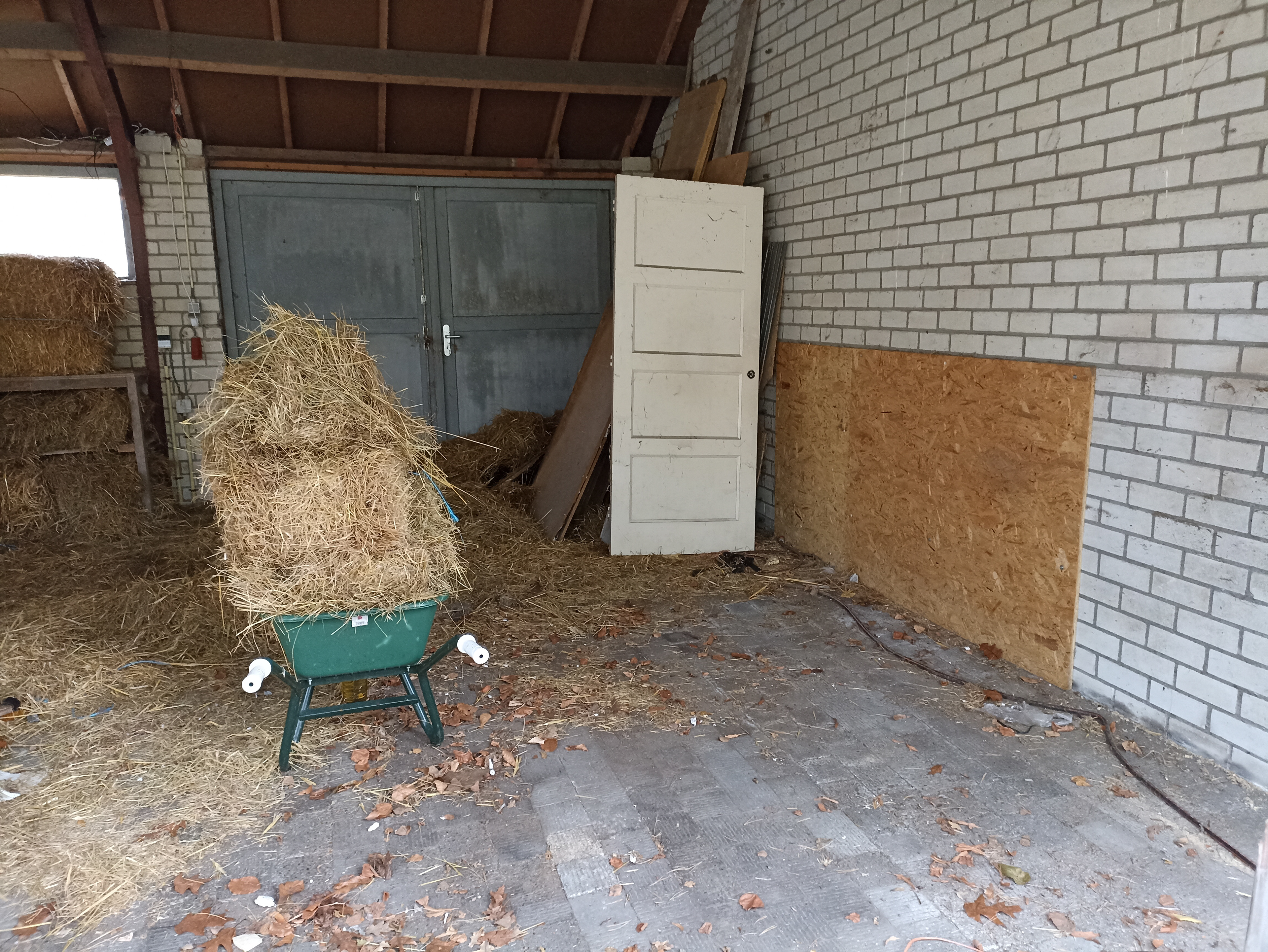
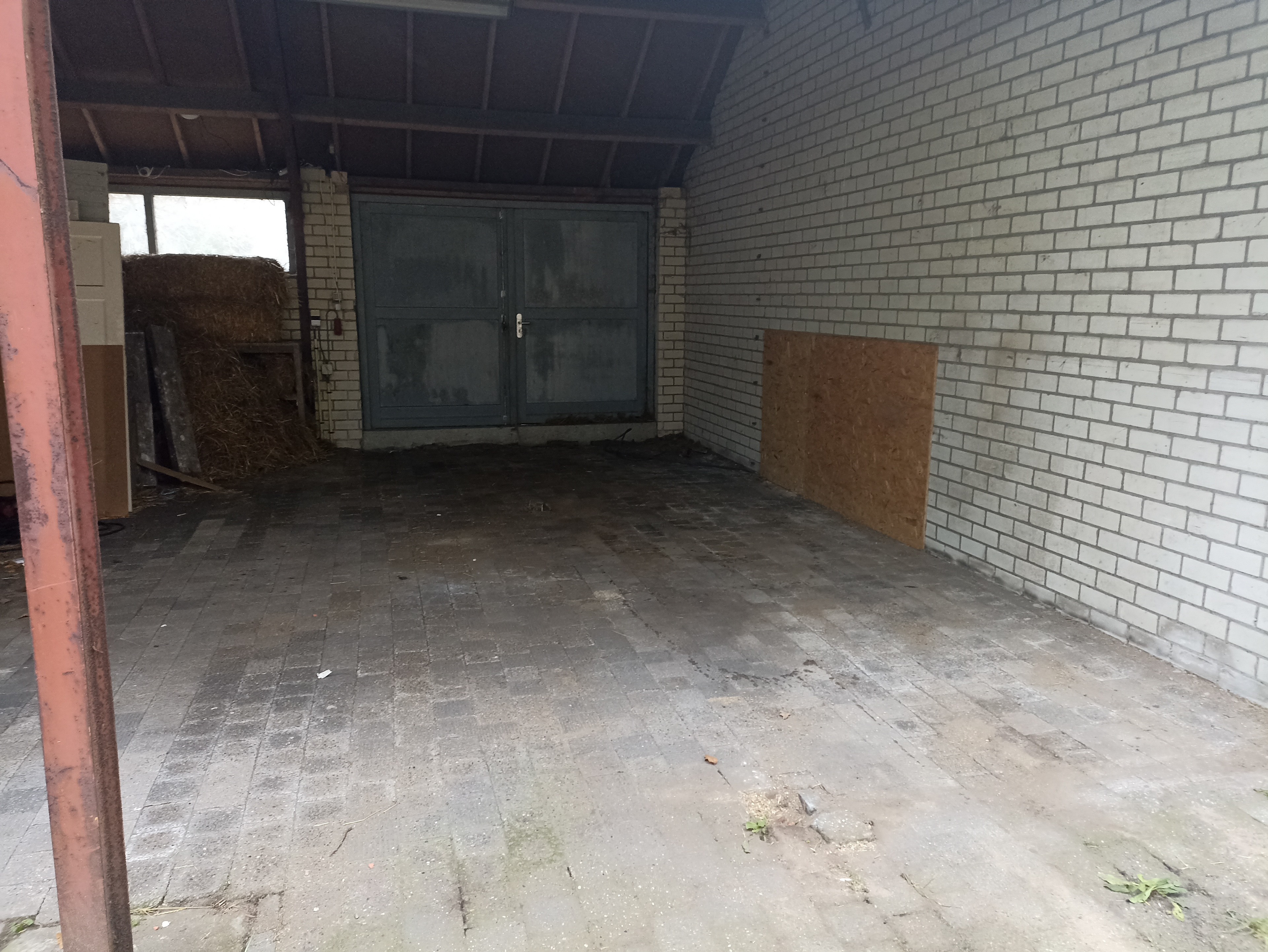
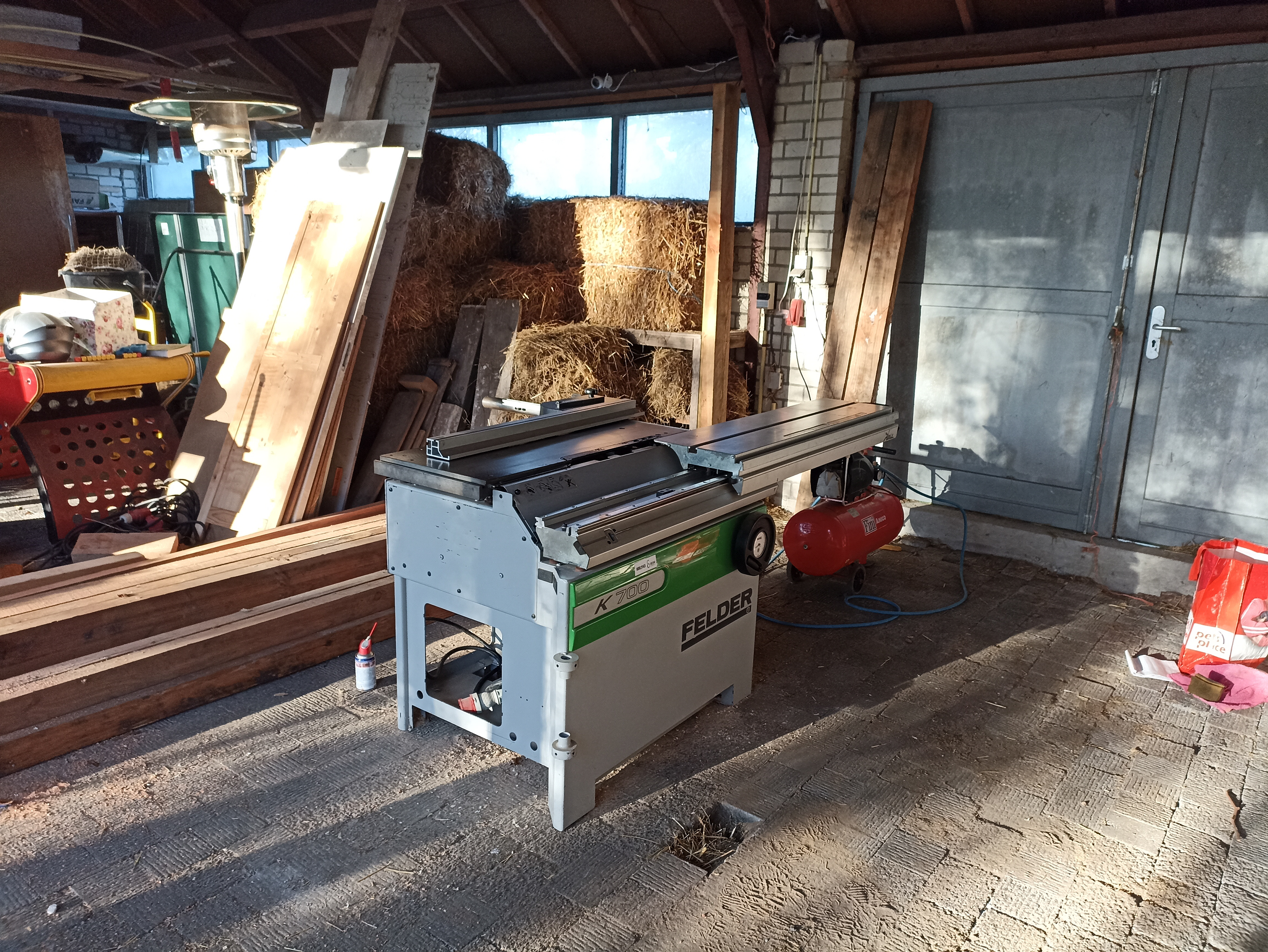
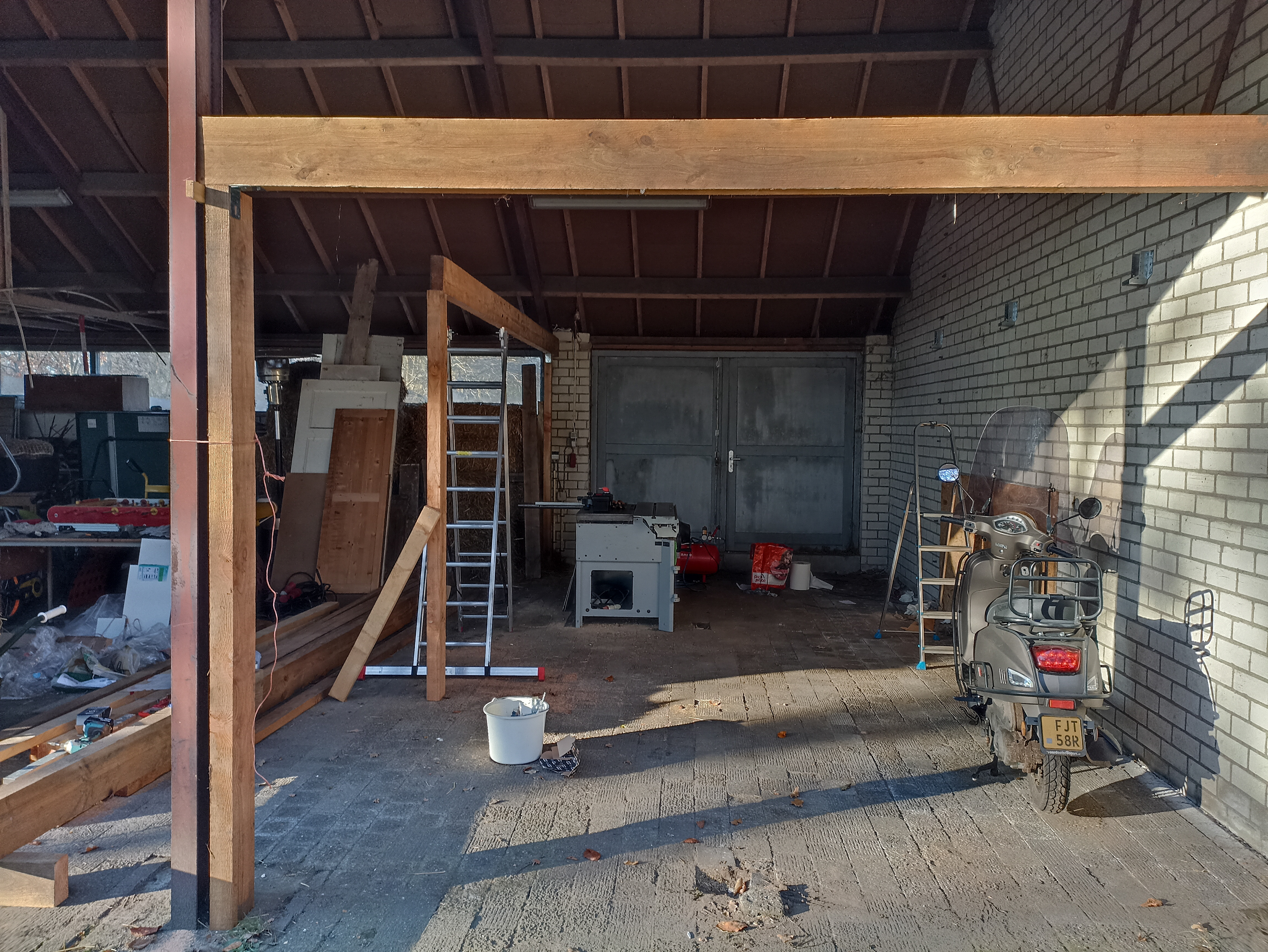
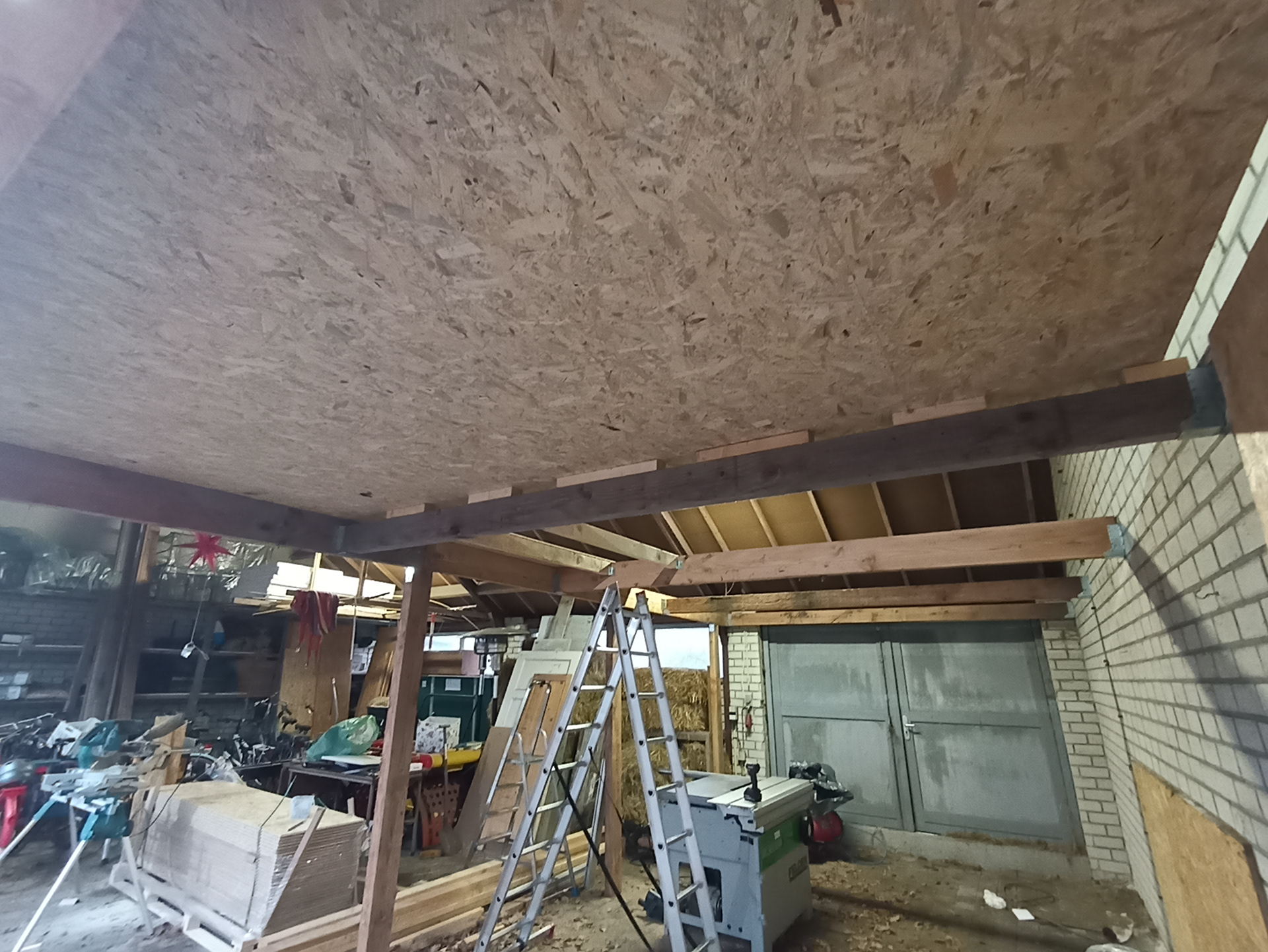
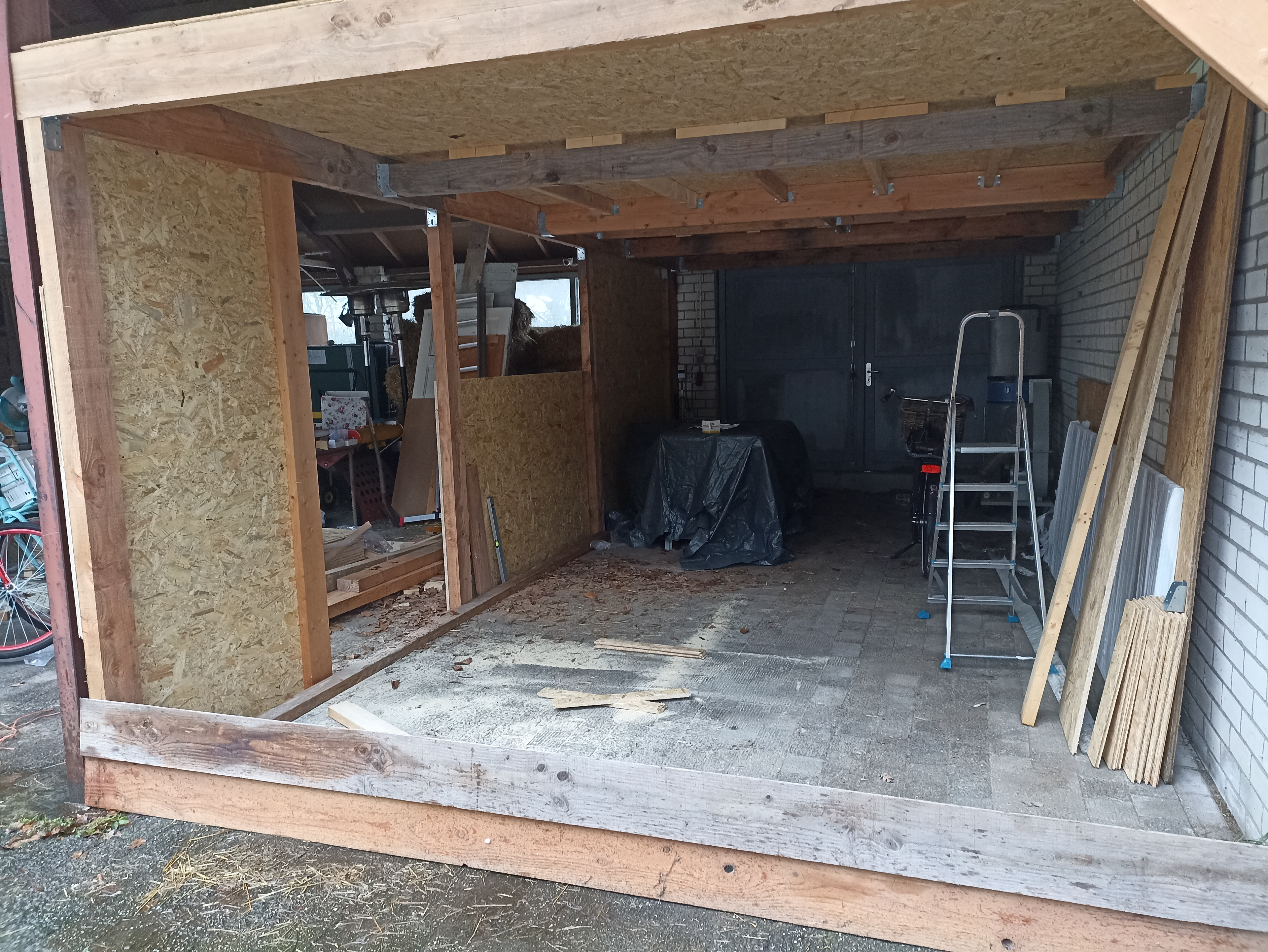
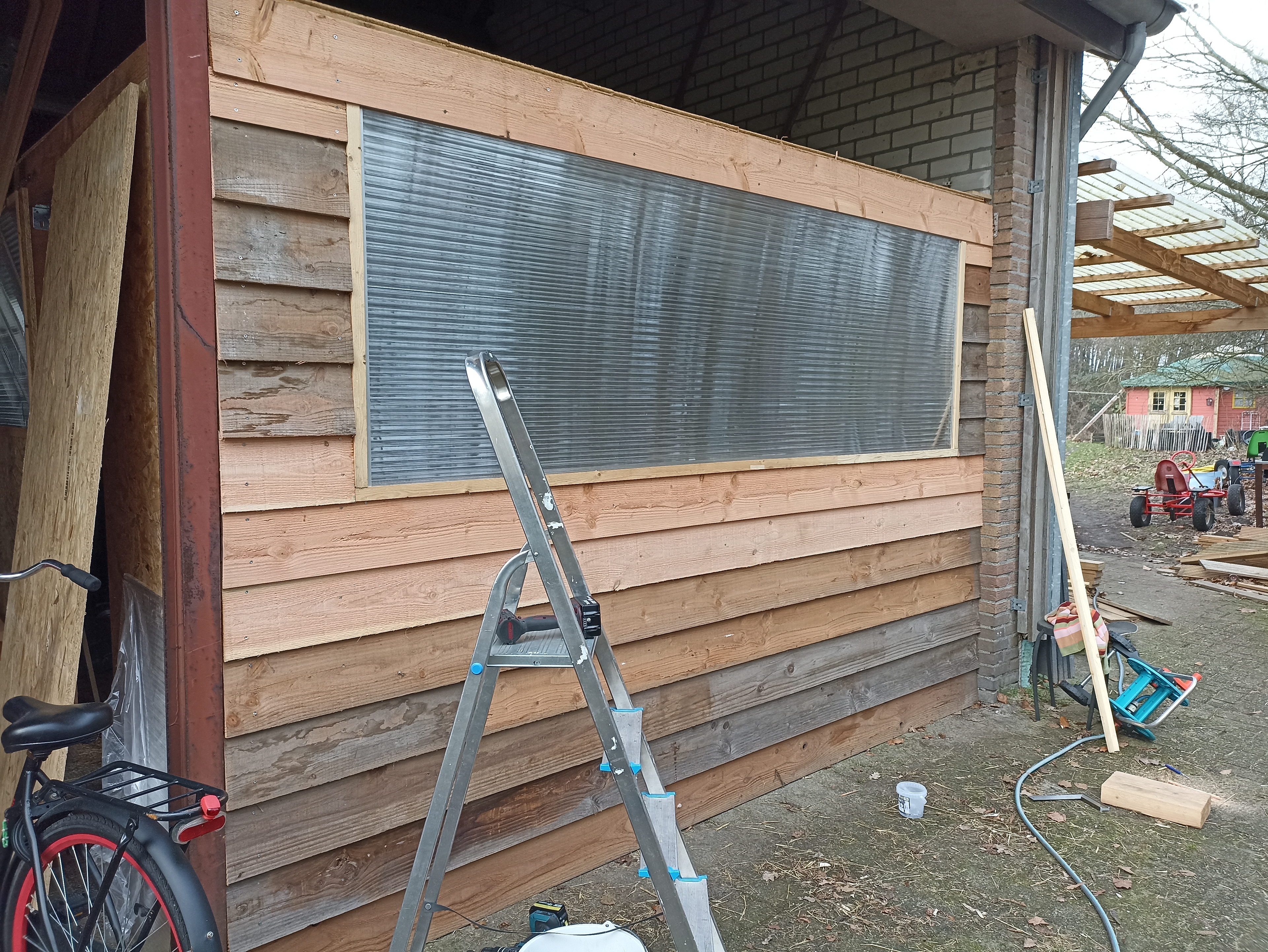
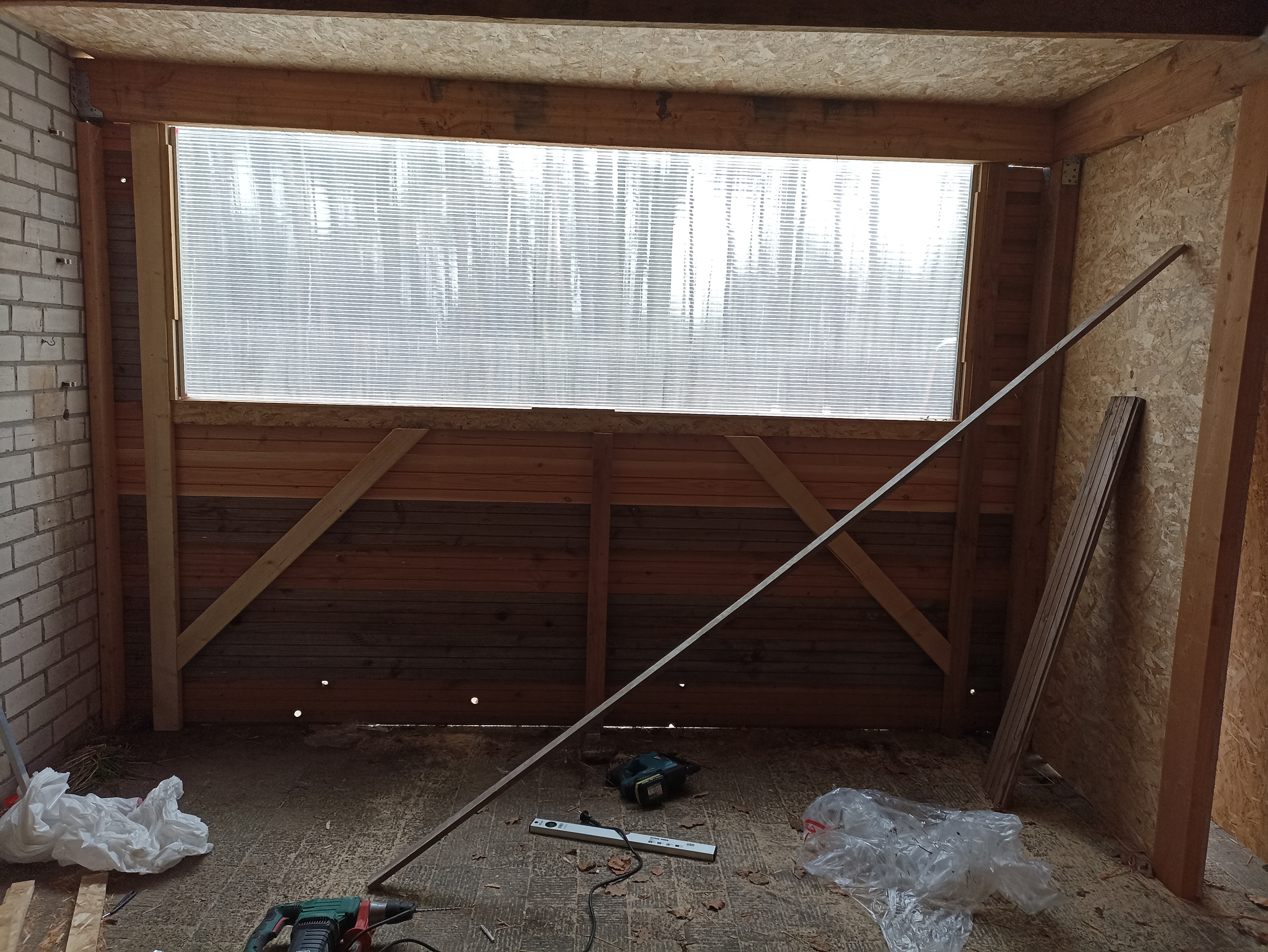
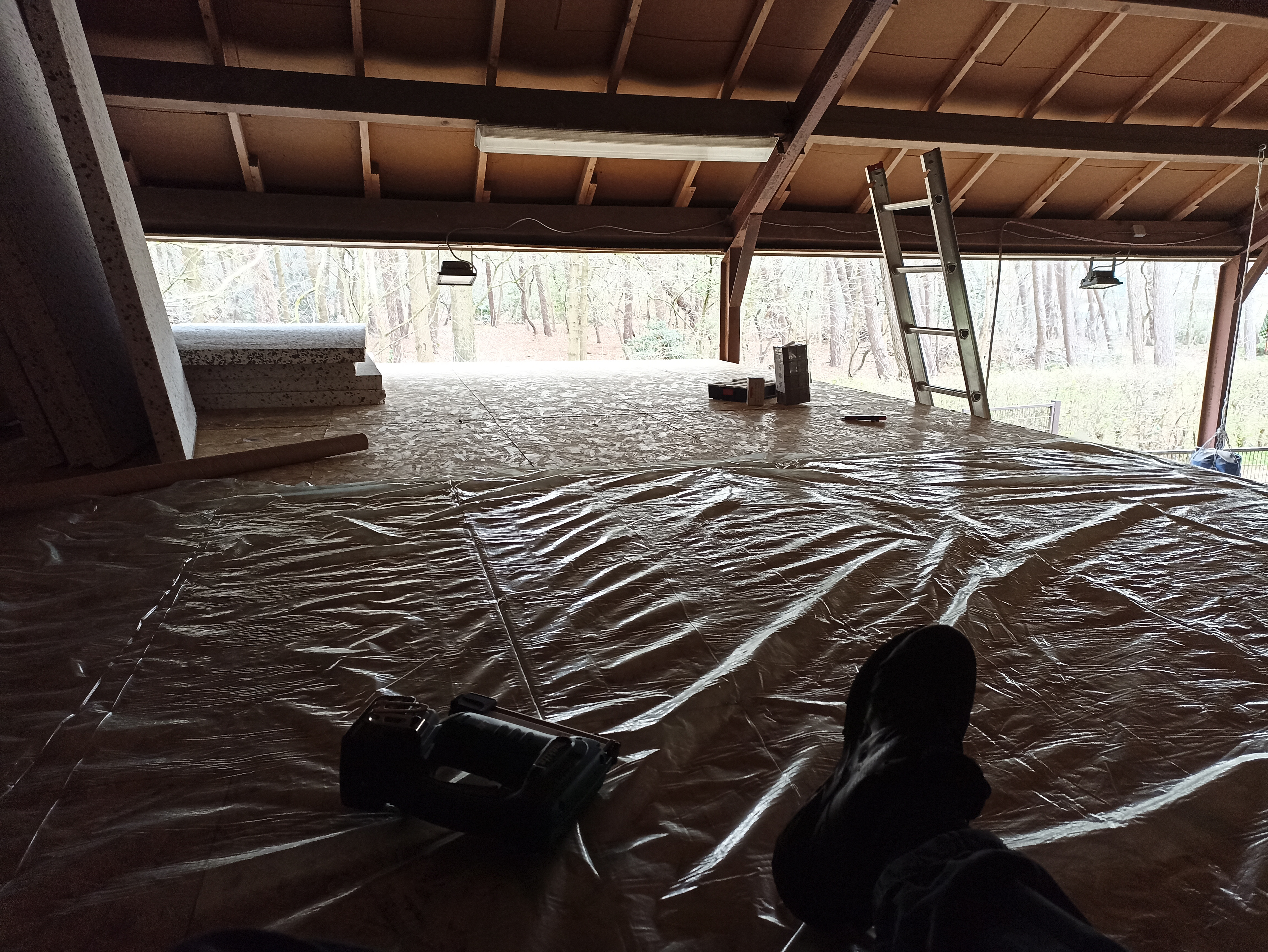
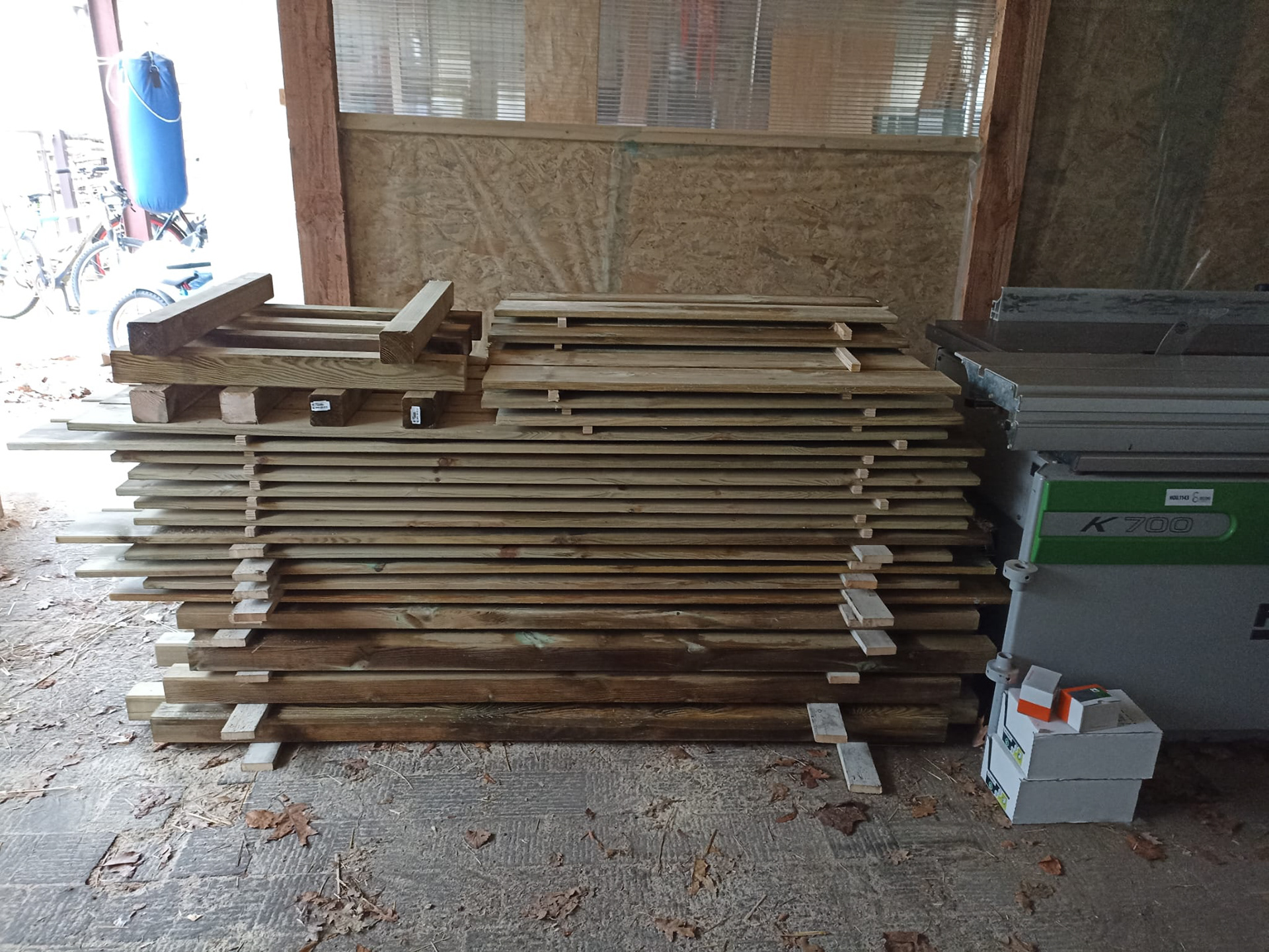
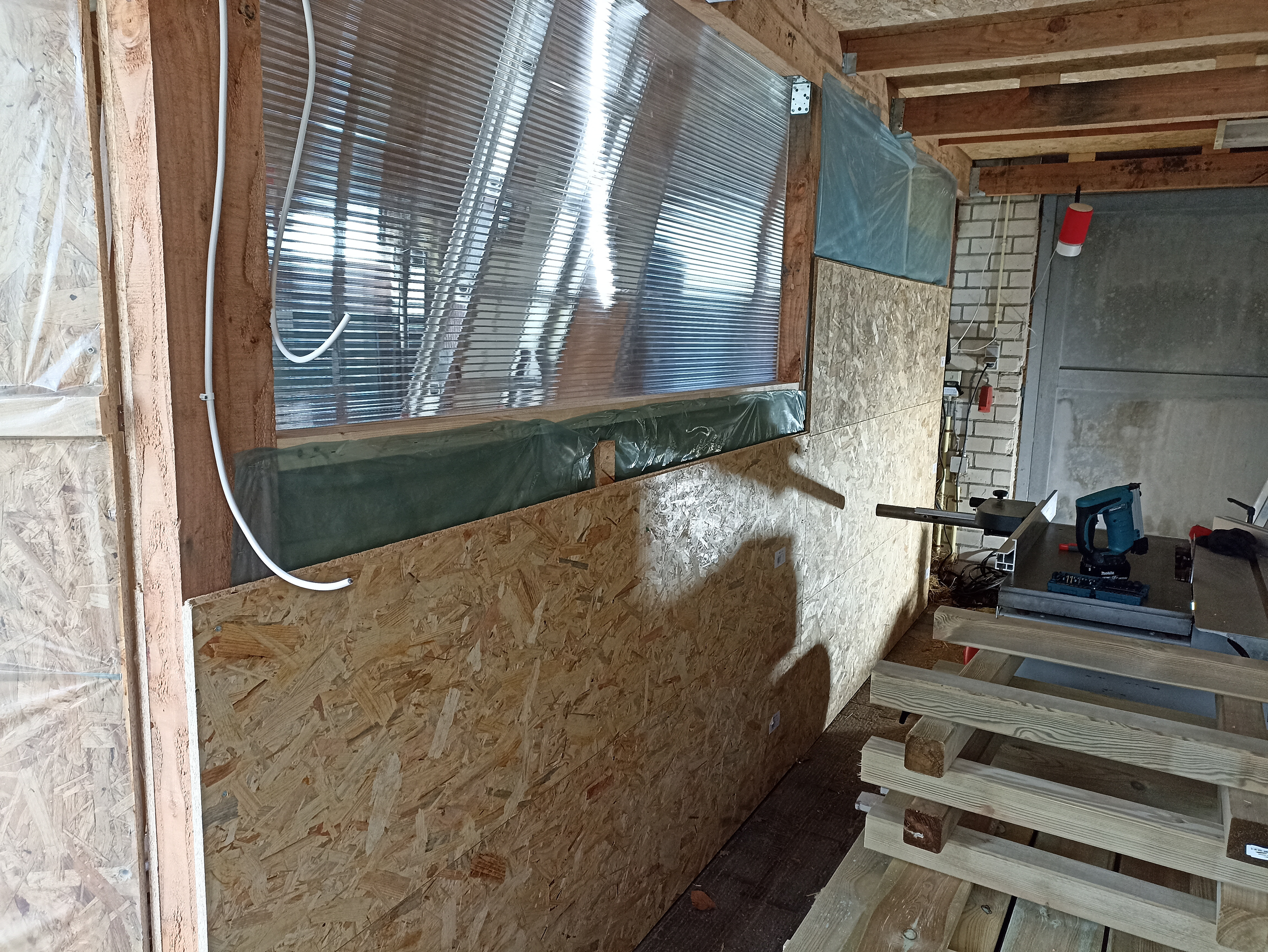
I decided not to work on this commission full time since I had quite a manageable planning, but instead to work on the shop itself one day a week as well. Here I started insulating the walls. If you know how to do it, it's quite easy and doesn't even take that long. It's a very important step though since working in the cold is very unpleasant and can even be bad for tools and materials.
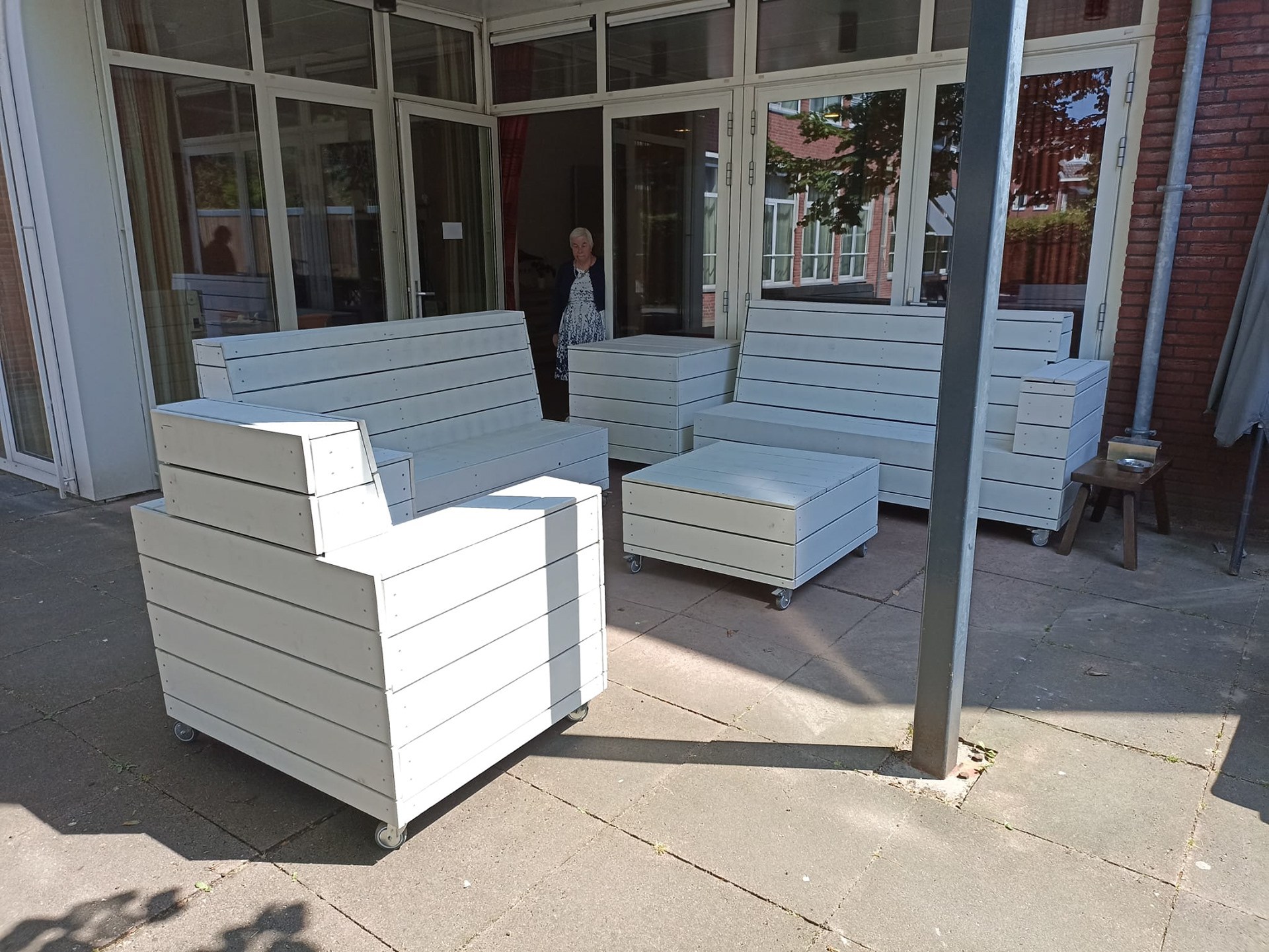
This order only just fit in my empty workshop, so when it was finally finished I was very happy. Not only with the result, but I could finally work on the place itself again which was definitely needed.
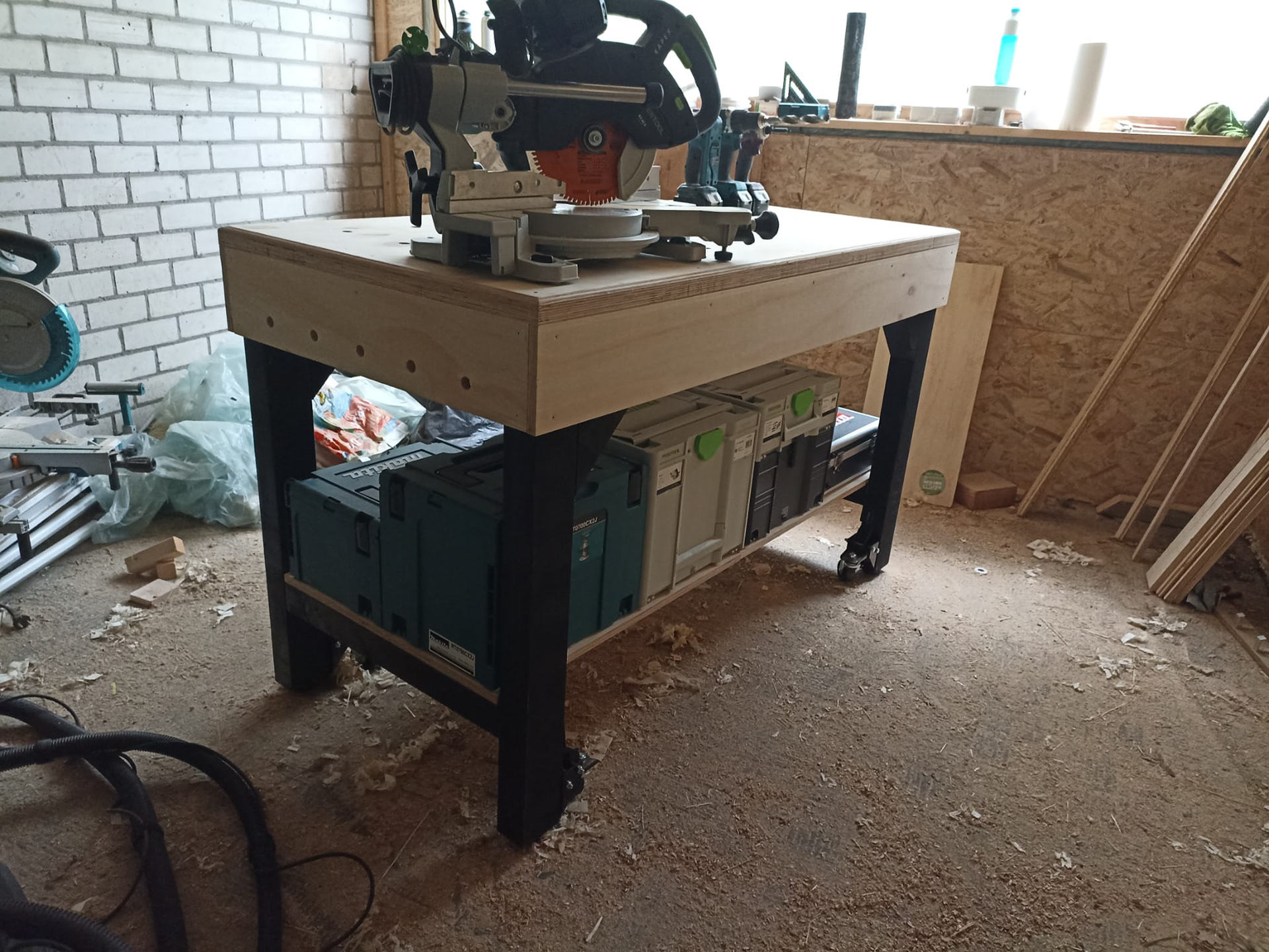
After having made an entire project without a workbench I decided I needed to build one. It's the most used tool in most shops and by making it yourself you can build it according to your needs. I wanted to have storage area for my tool boxes and dog holes in both the top and side. Later on, I added a french cleat to the other sides so I can hang tools on them if I use them in a project. I have the same french cleat system on my walls, so some tools can be hung at different places.

Finally having a workbench, I decided to build a guitar for myself. Definitely not the right decision at that time, but it had always been a dream of me to make a guitar. This project took a really long time because I found I didn't actually have the time for it. It's now finished though, and has its own project page.
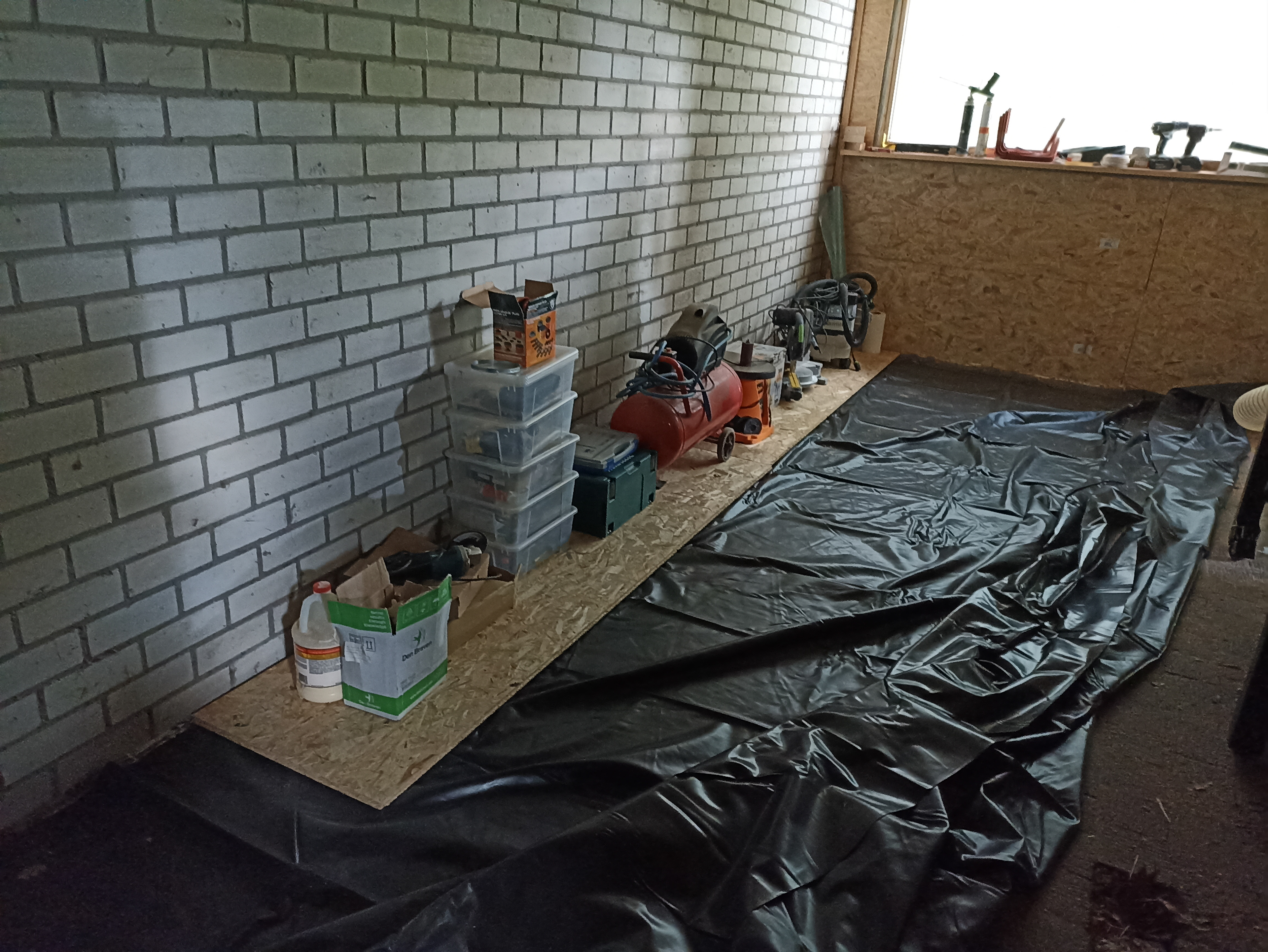
The stone floor was cold, uneven and moisture was slowly coming up through the seams. This all made it a bad surface to work with, so I decided I needed to lay some new flooring on top of it. I needed to empty the place again and started working from one corner. I had been delaying this step for far too long and I was actually really happy I finally took the decision to start, even though it meant pausing my guitar build for a while.
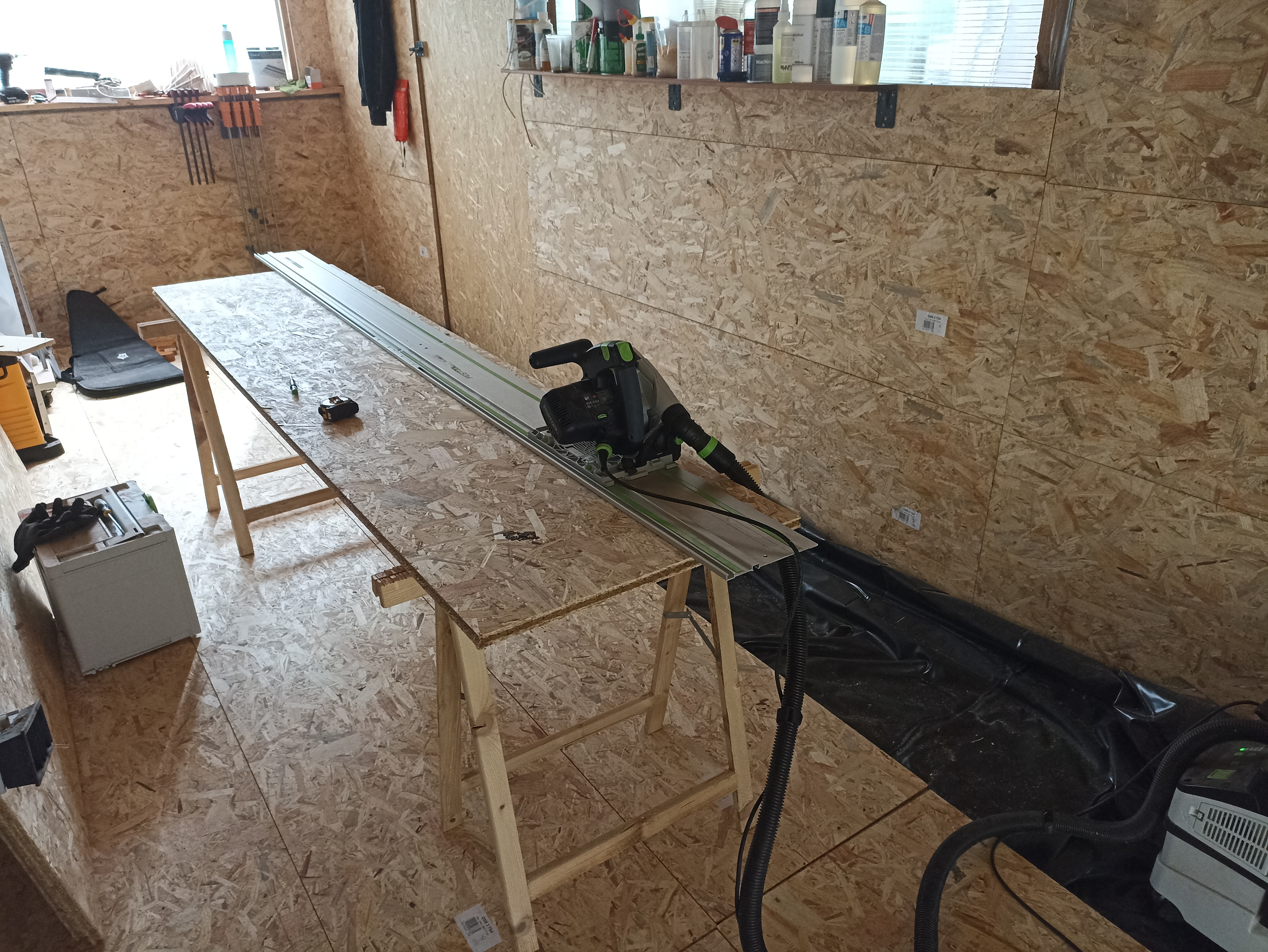
This step went a lot quicker than I expected. Some sheets needed to be cut down to size, but I managed to get the entire flooring done in about a day. Although it's a lot of OSB, it was getting a lot nicer of a place to be than before with the stone flooring. I probably want some sort of PVC flooring at some point, but I don't know when I'll have the time for that. This will do for now.
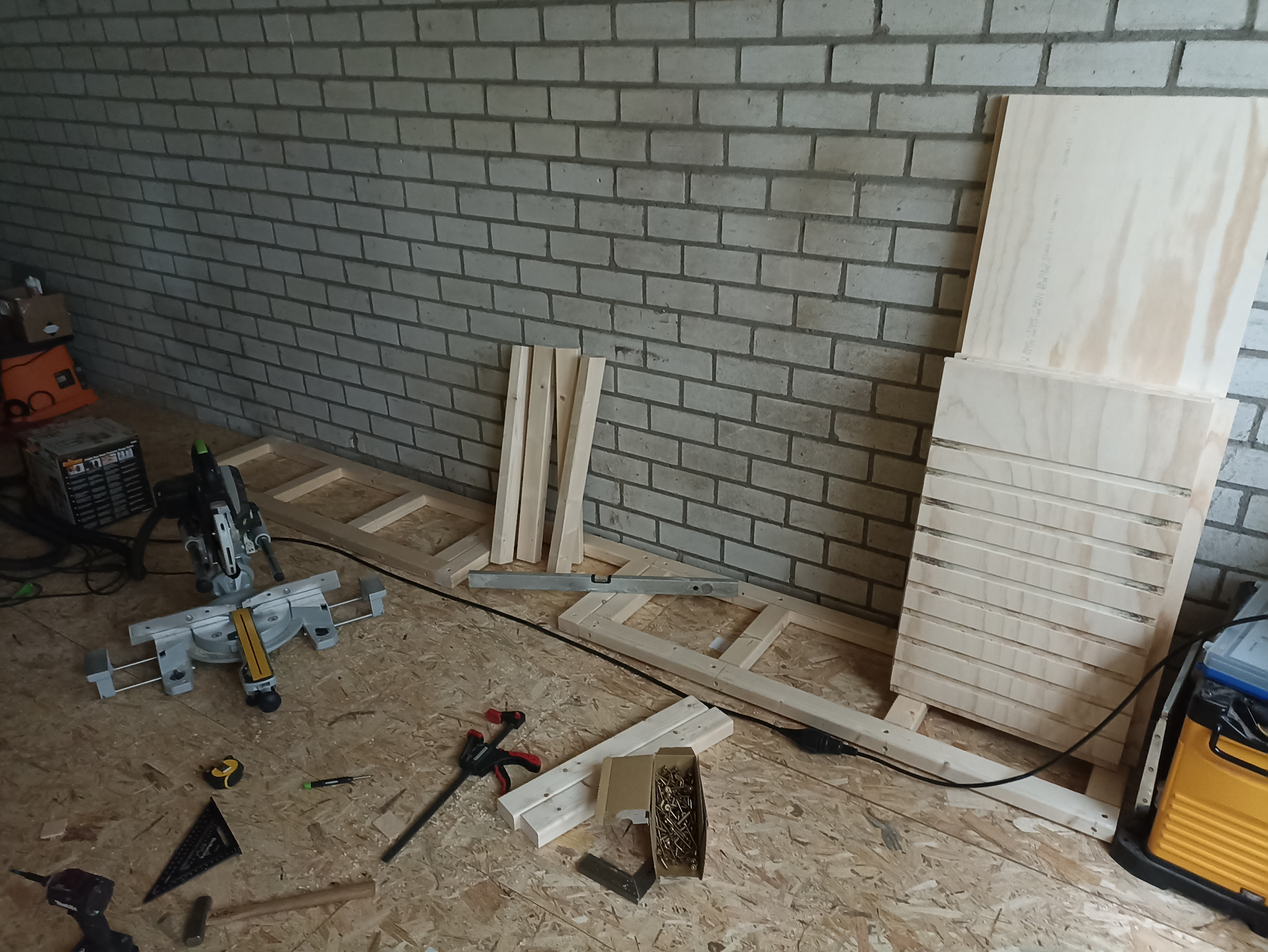
With the new flooring laid down it was finally time to build some shop furniture and storage. Since the original stone floor was uneven and not level, my flooring wasn't either. A miter saw station absolutely needs to be level though, so I needed to shim the frame.
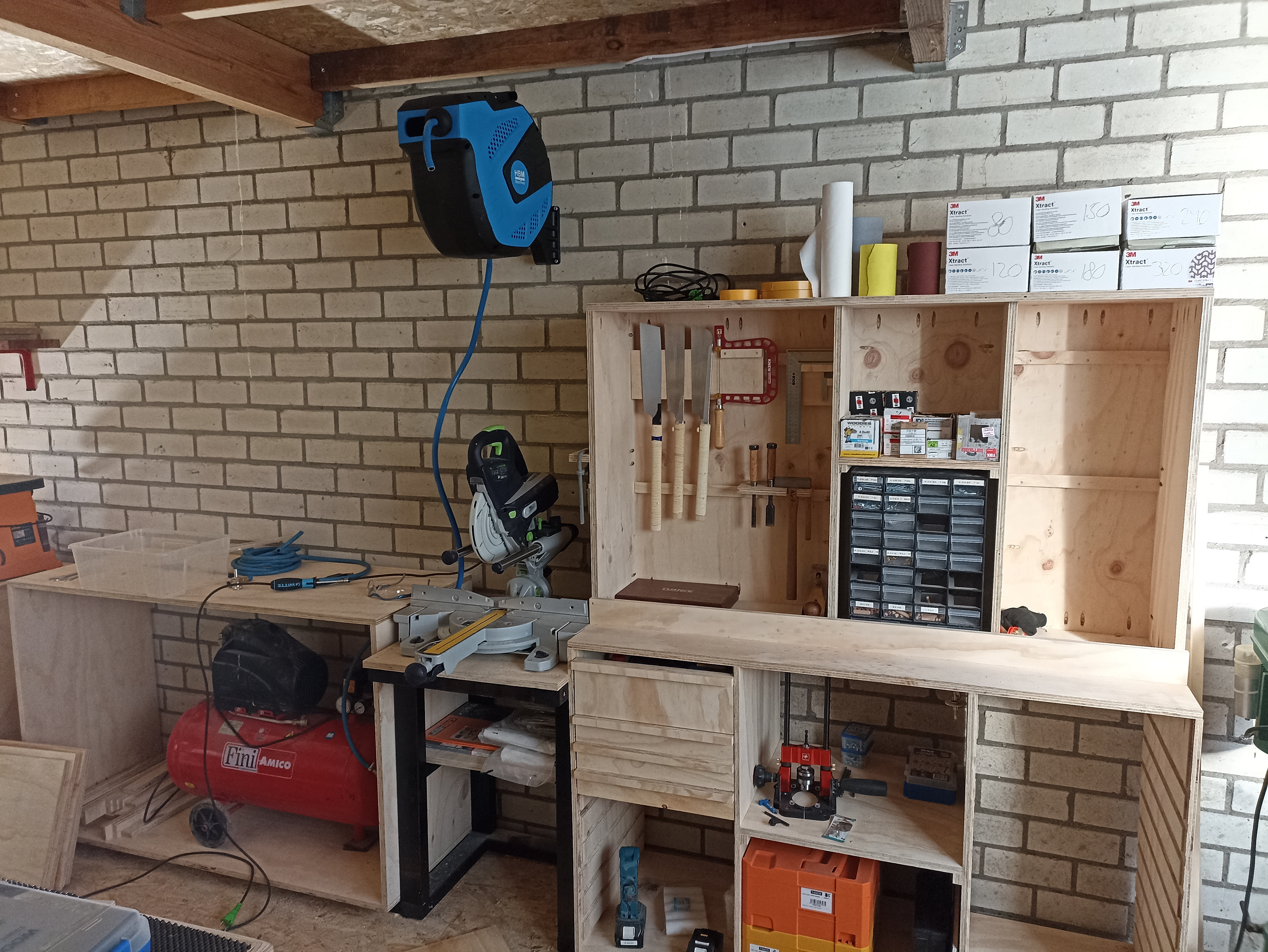
This miter saw station would be my main storage wall as well. I made the drawers to standard sizes so they would be interchangeable. Some cabinets have french cleats so the tools on them can also be hung at different places, even on my workbench. Organizing any workplace is very important to get a good workflow. if you need a tool, it's best to be able to find it quickly.
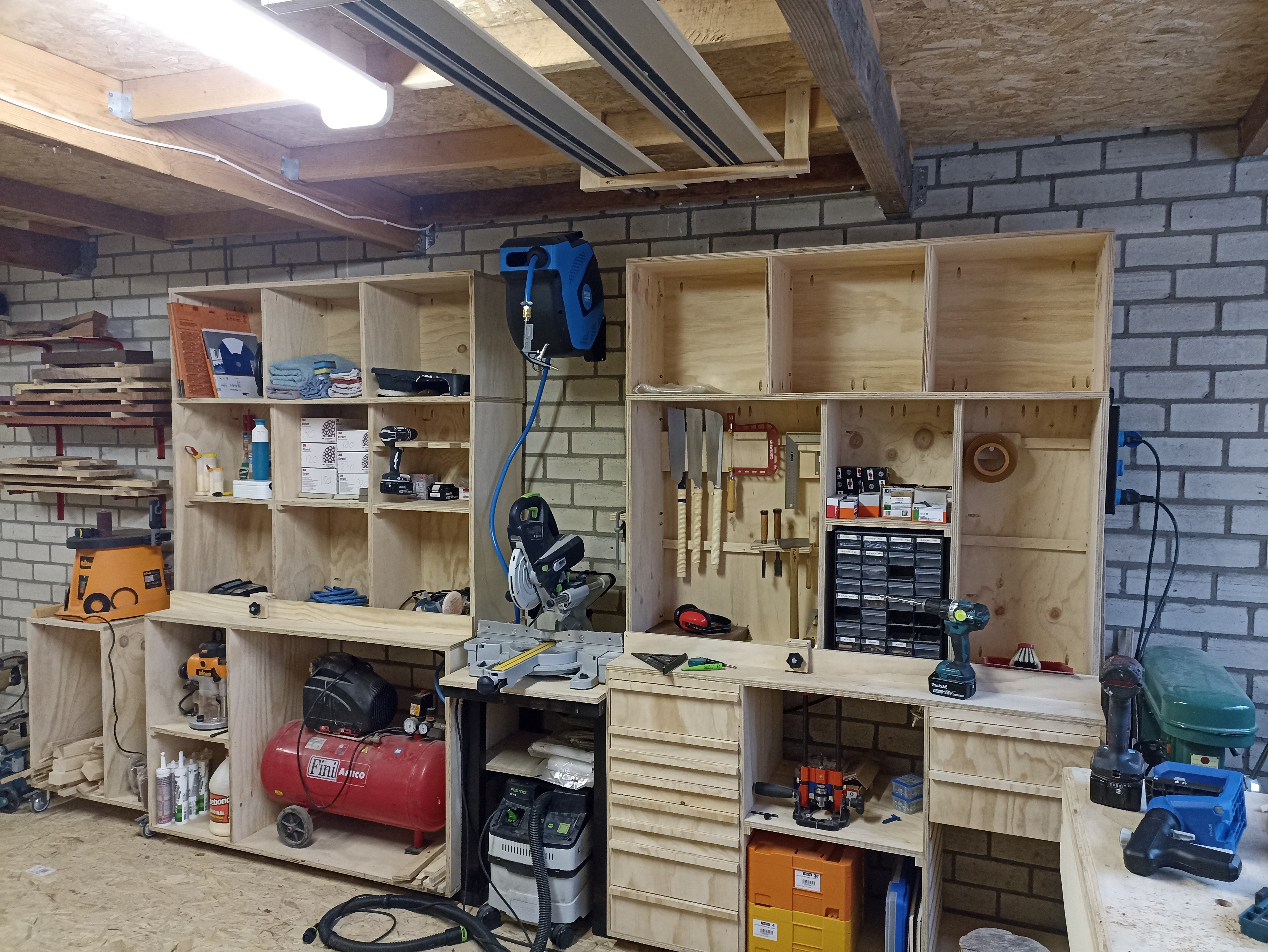
I decided to add an extra layer, even though I didn't have anything to store there yet. Over time the new room will be filled which keeps the shop as clean as possible. i prefer not to have anything laying around that I don't need at that specific moment. Even roof space can be used to store things, like the tracks for my track saw.
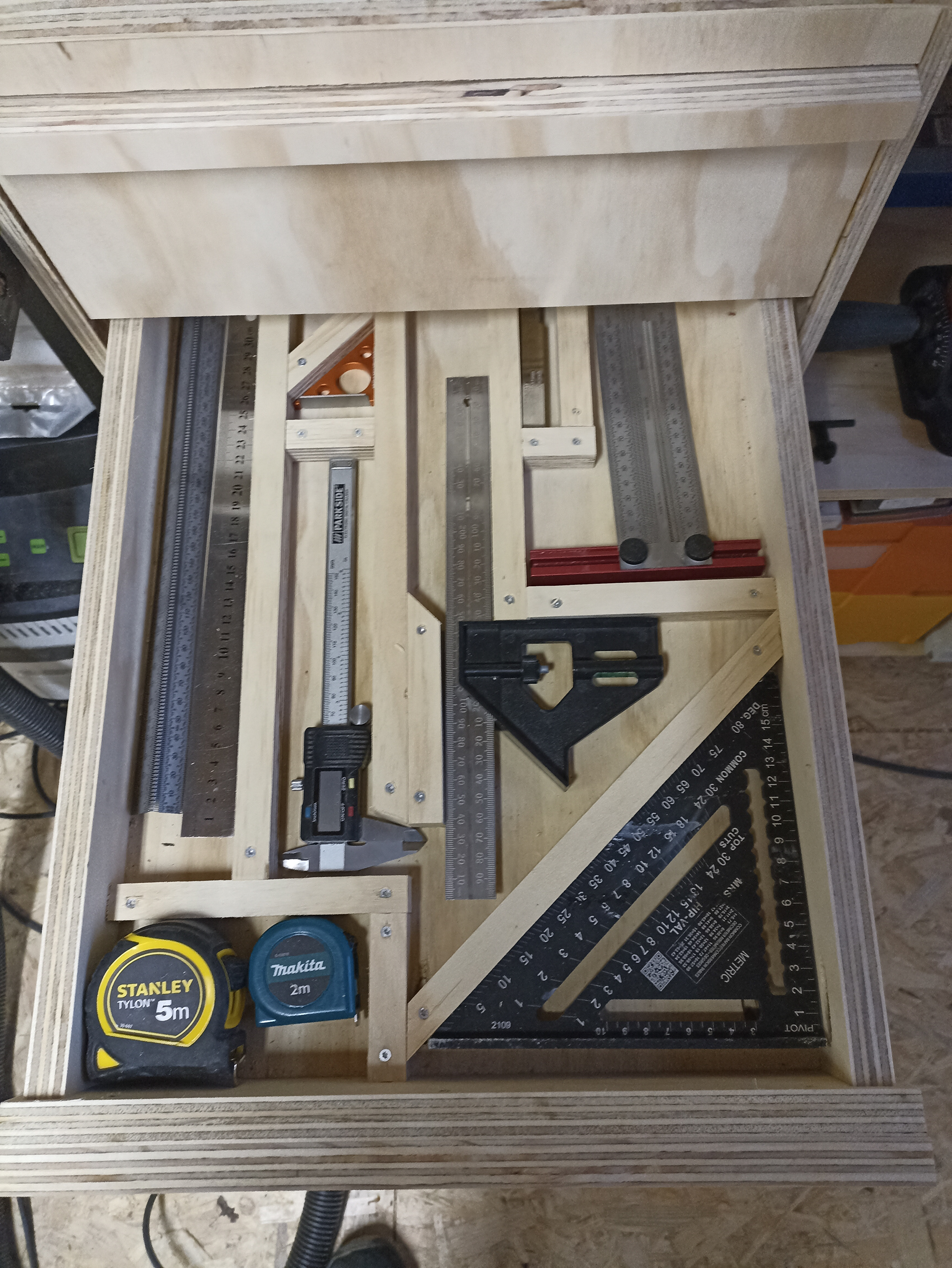
By organizing the drawers this way I know that every tool will always be in the same place. If I need a tool I'm always able to find it quickly.
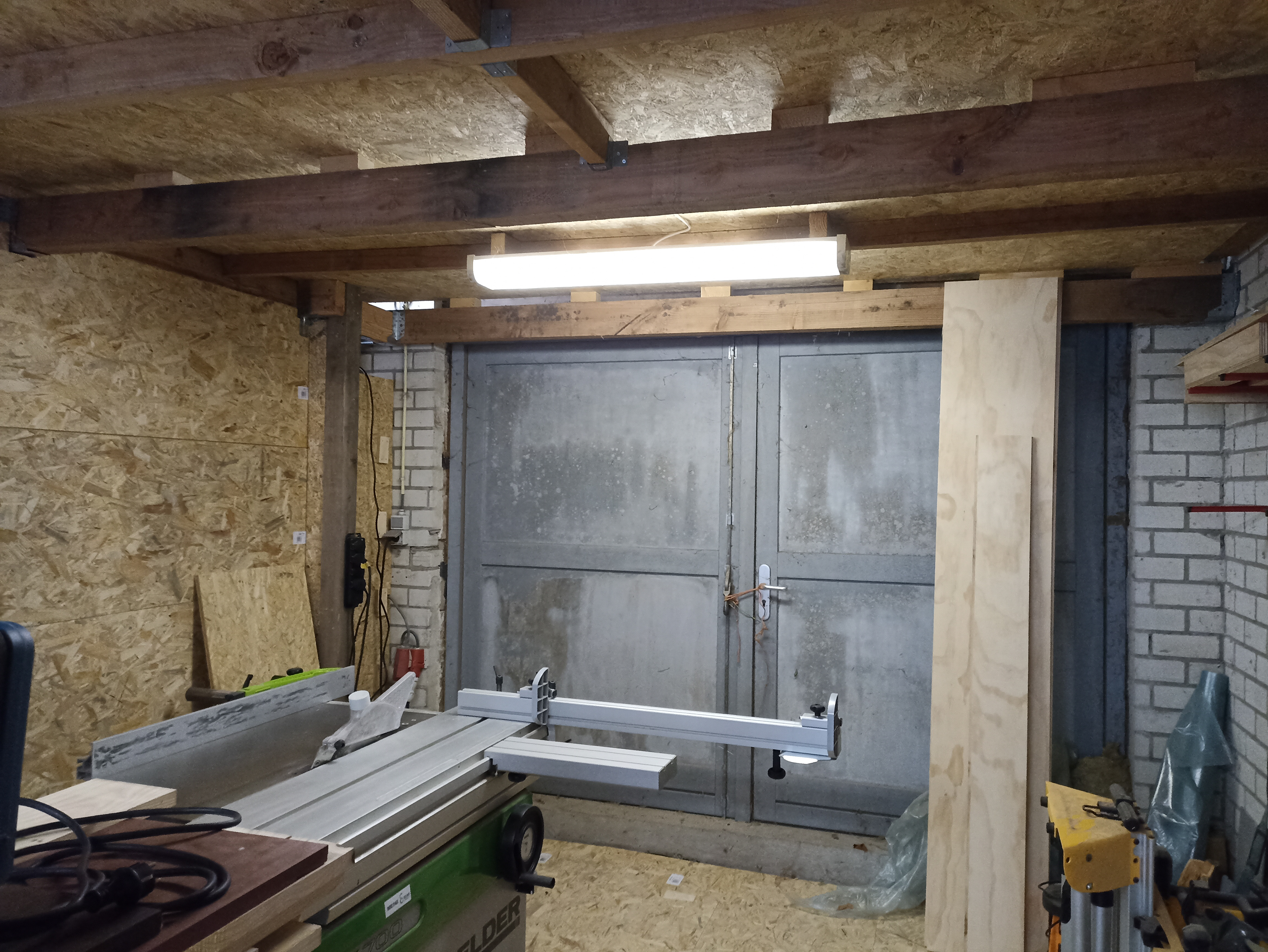
Up until this point I used a construction lamp if the sunlight wasn't enough. As winter came though, it got darker and I needed more lighting. I got some help to install some lighting and new outlets, which made the shop much more functional.
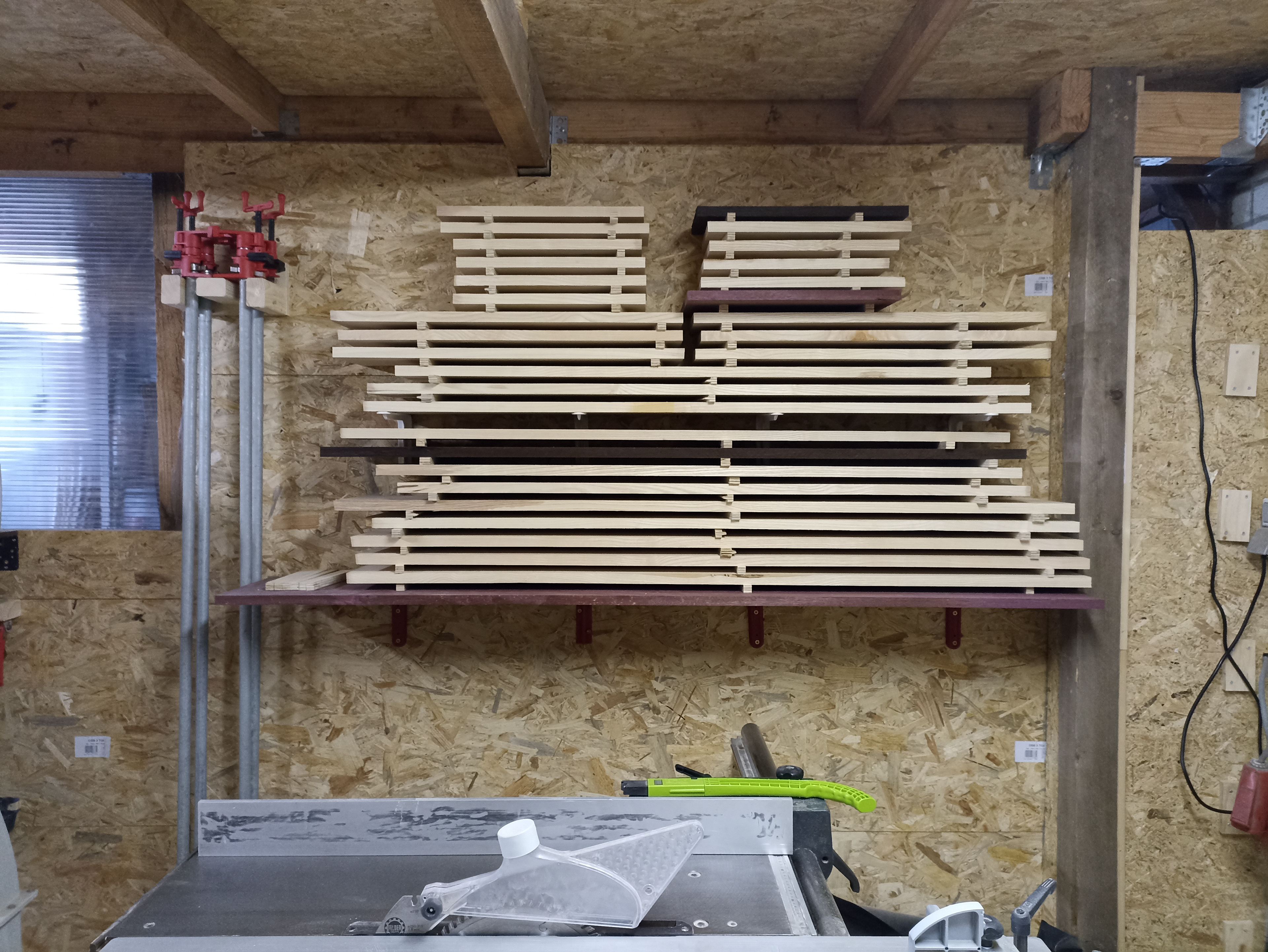
A lumber rack is very important as a woodworker. On this side I store my most used hardwoods, on the other side I store my more exotic hardwoods. Currently I have a lot of Ash and some Wenge and Purperhart for a commission I'm working on.
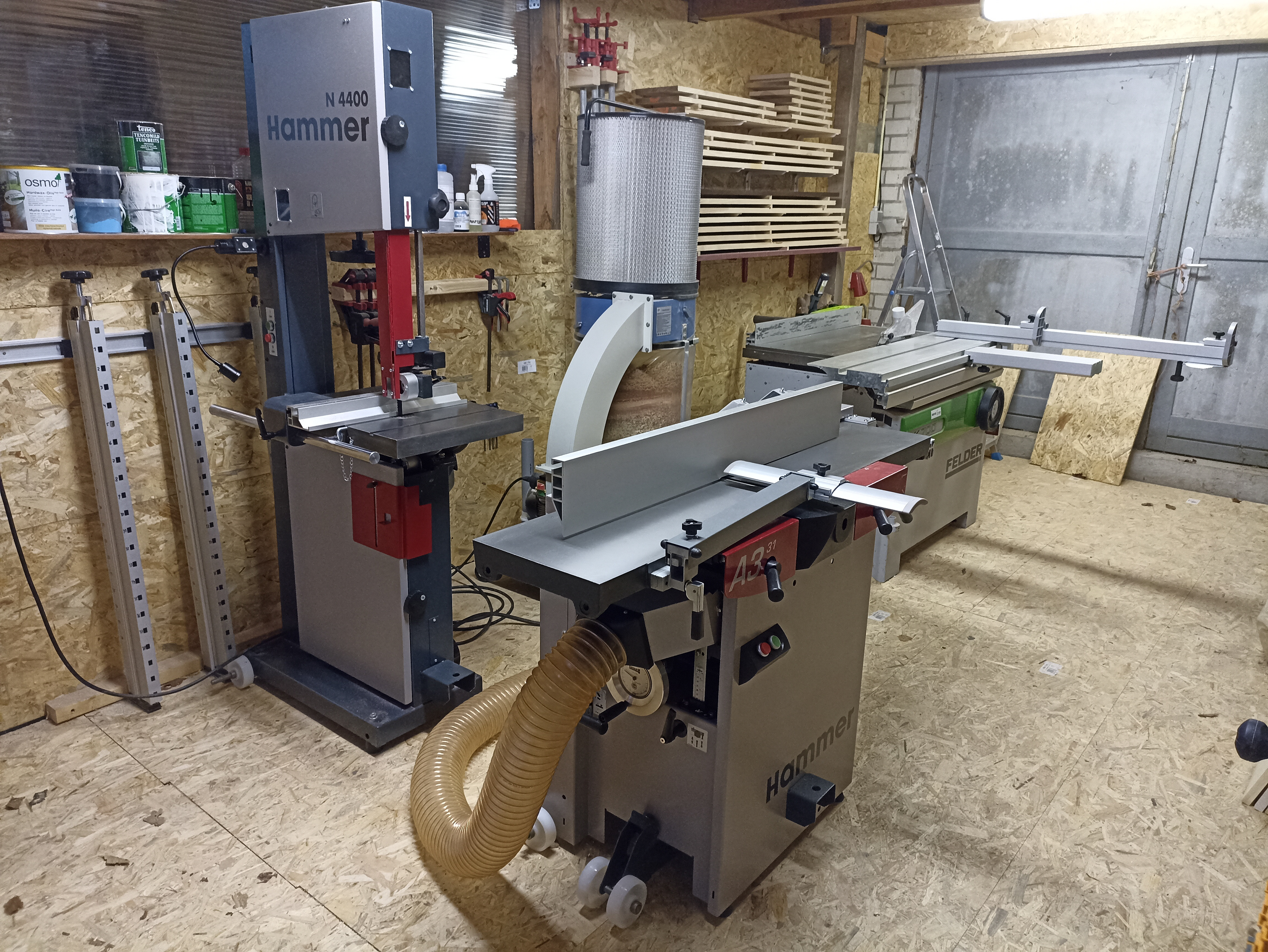
Woodworkers never stop buying tools. Big and expensive tools aren't necessary to make beautiful things, but they do make it much easier and often faster, more accurate and more enjoyable.
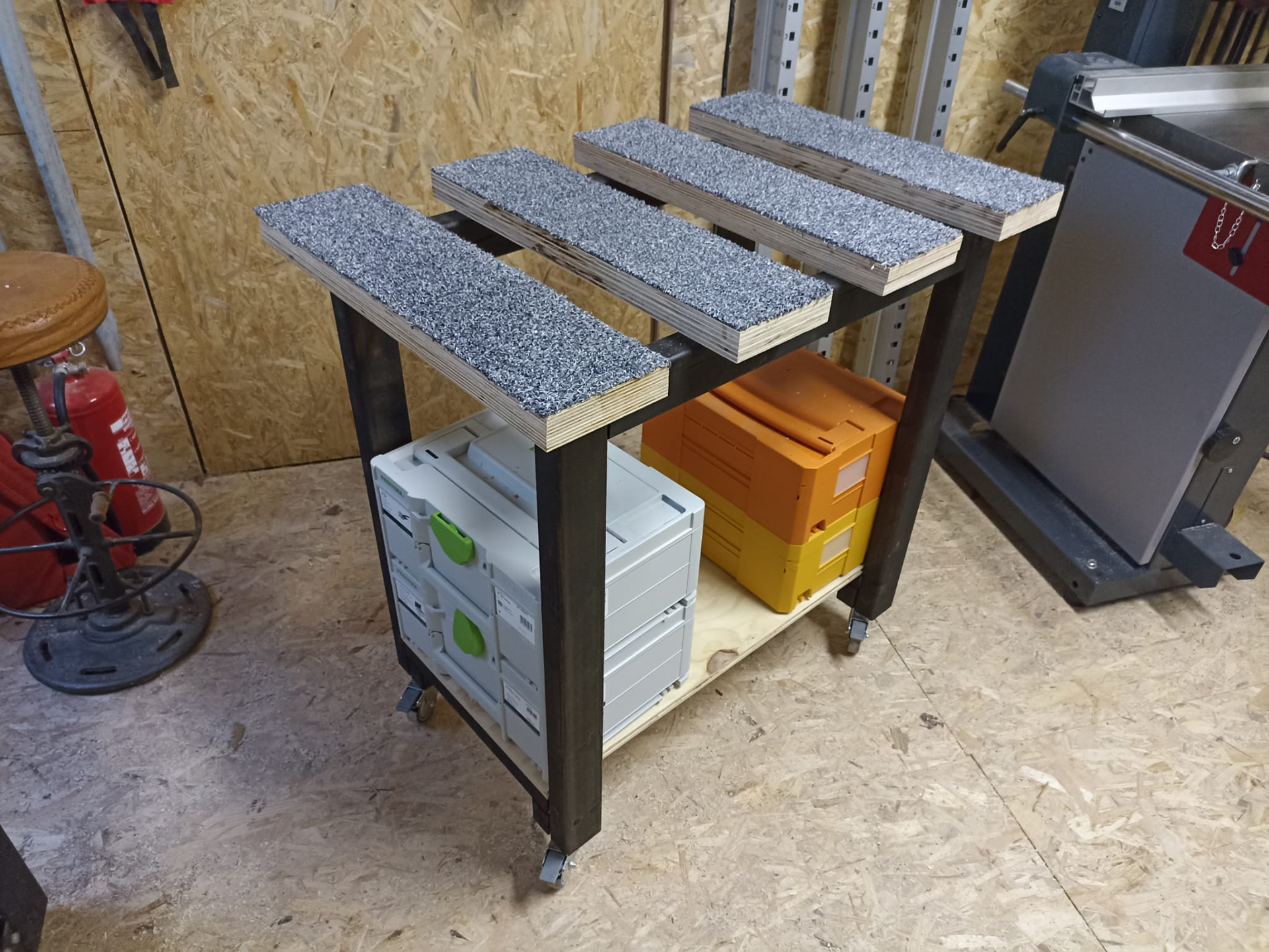
While working on a project, I realized I could use a moveable shop cart. This is a very simple cart and was really fast and easy to build, but it serves multiple purposes.
While using the jointer or planer I have a place to put the wood down in between the several passes. It's also a very handy cart for finish sanding, since the soft surface of the carpeting makes sure the wood doesn't scratch while also giving a good grip to prevent it from sliding around. The gaps in between the carpeted plywood makes it easy to get clamps around so it's also a great place for glue-ups. Since it's on wheels I can put it in a corner when something is drying or when I don't need it. This cart only took me a couple of hours to make, but it makes many processes in the workshop much easier.
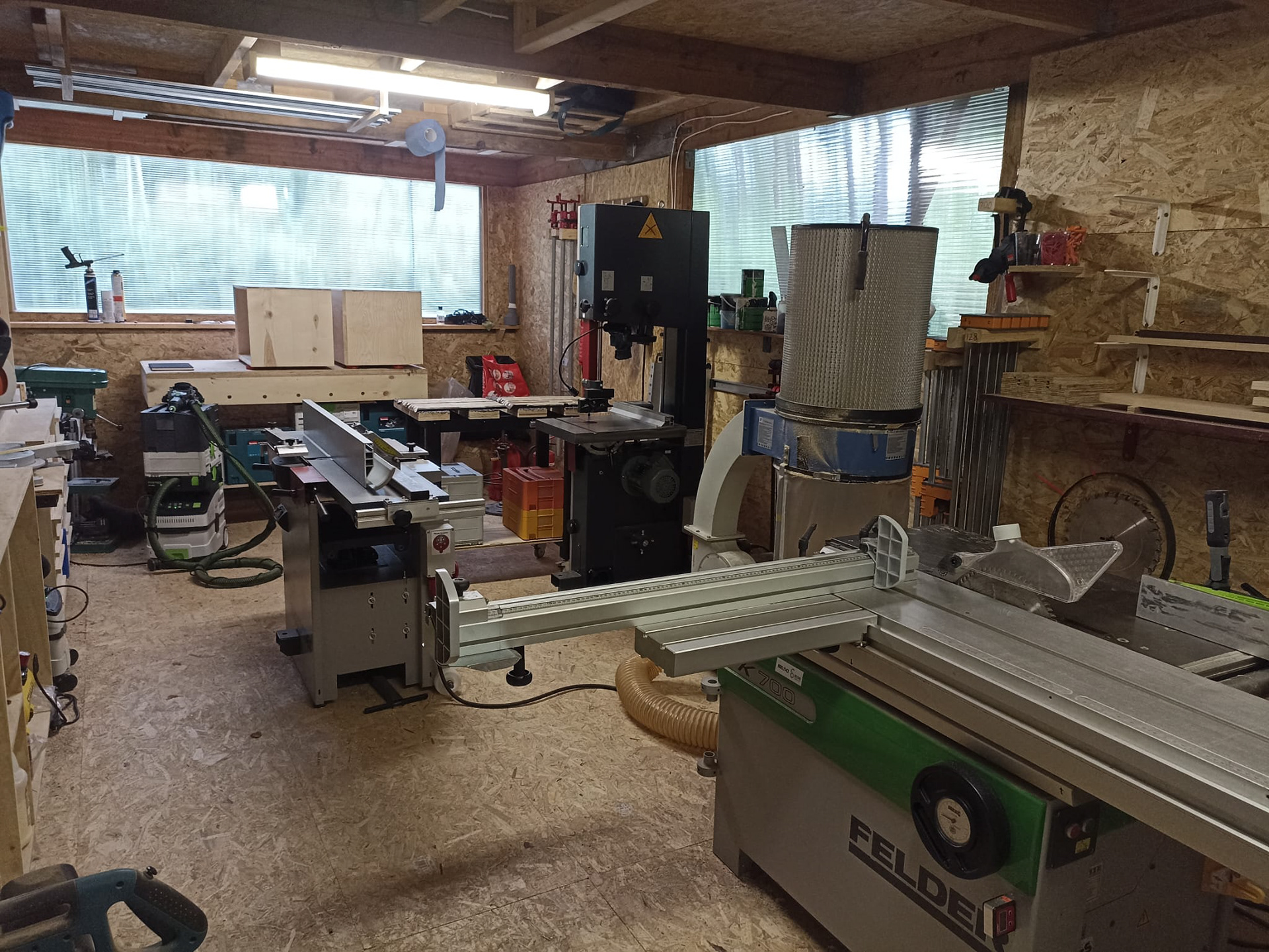
This is what the workshop looks like right now, in May 2024. I've made lots of progress but there are still some things to do.
I'm currently working on a commission, but when that's done the next step will probably be the ductwork. I now have a flexible hose I can attach to each tool which does work, but isn't ideal. Getting proper ducting will make switching from tool to tool much less work. I also want to make a cart for my drill press, a router table and get some pvc flooring or carpeting at some point. These are some small projects you'll most likely see in the future. From now on nothing is absolutely necessary since the workshop is functional, but things can always be improved.